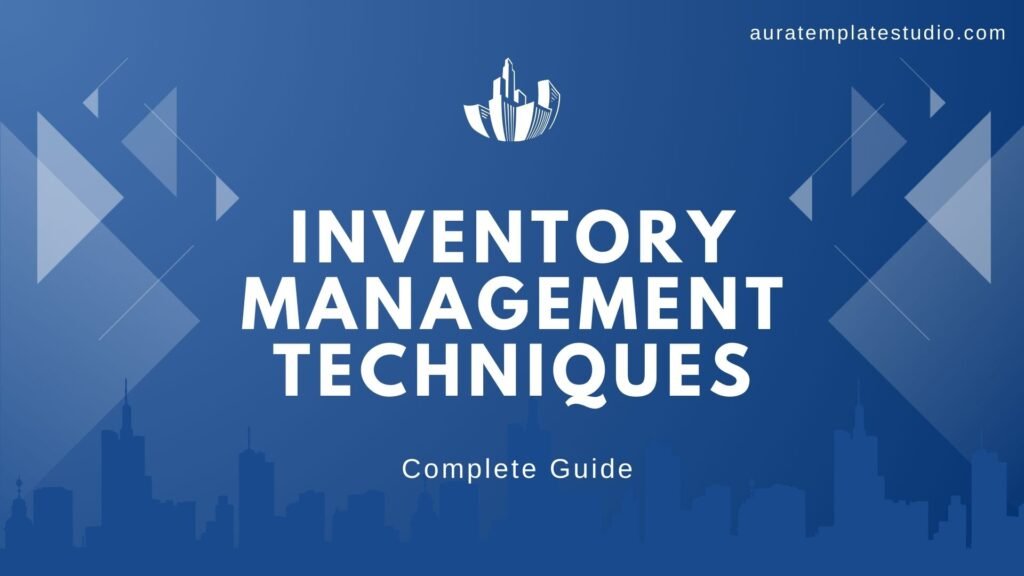
Core Inventory Management Techniques
✅ Mastering the Essentials: Proven Inventory Management Techniques
In my experience, businesses that get the basics right are often the ones that scale smoothly. Core inventory techniques like First-In, First-Out (FIFO) and Last-In, First-Out (LIFO) aren’t just academic—they directly impact shelf life, cost of goods sold, and tax implications. FIFO, for instance, is crucial in industries where products expire, like food and pharmaceuticals. If you’re not already applying this method, it’s a game-changer for reducing waste and improving turnover.
Another essential technique? Just-in-Time (JIT). I’ve seen smaller businesses slash holding costs dramatically by moving to JIT with strong supplier relationships and real-time stock monitoring.
👉 Tip: Start with FIFO if your products are perishable, and move toward JIT only when you have reliable data and vendors.
📦 Inventory Control 101: Techniques Every Business Should Know
Let’s talk reorder points and economic order quantity (EOQ). These two formulas are the foundation of inventory control. Reorder points tell you when to restock, and EOQ helps you figure out how much to order to minimize total costs (ordering + holding). It’s surprising how many businesses still use gut instinct instead of simple math!
Here’s a practical example:
If your daily sales average 10 units, and lead time is 5 days, your reorder point is 50 units. Build a buffer into that if demand is volatile.
Also, cycle counting—counting portions of your stock regularly instead of doing one massive year-end count—helps keep data accurate and minimizes downtime. In one warehouse I worked with, implementing weekly cycle counts cut inventory errors by 40%.
👉 Tool tip: Use Google Sheets or inventory software like Zoho Inventory or inFlow to automate your reorder alerts and tracking.
🌀 From Chaos to Control: Simplifying Inventory with Proven Methods
If inventory feels overwhelming, you’re not alone. One of the fastest ways to restore order is to standardize SKUs, streamline naming conventions, and reduce the number of variants. I once helped a client go from 2,000 SKUs down to 1,200 without losing sales—just by eliminating duplicates and slow-movers.
Also, applying ABC Analysis can be a revelation. You’ll realize that 10-20% of your items (Class A) make up 70-80% of your value. Focus your control and attention there.
👉 Pro tip: Use conditional formatting in Google Sheets to visually highlight your Class A inventory—it’s a fast way to keep an eye on your highest-impact stock.
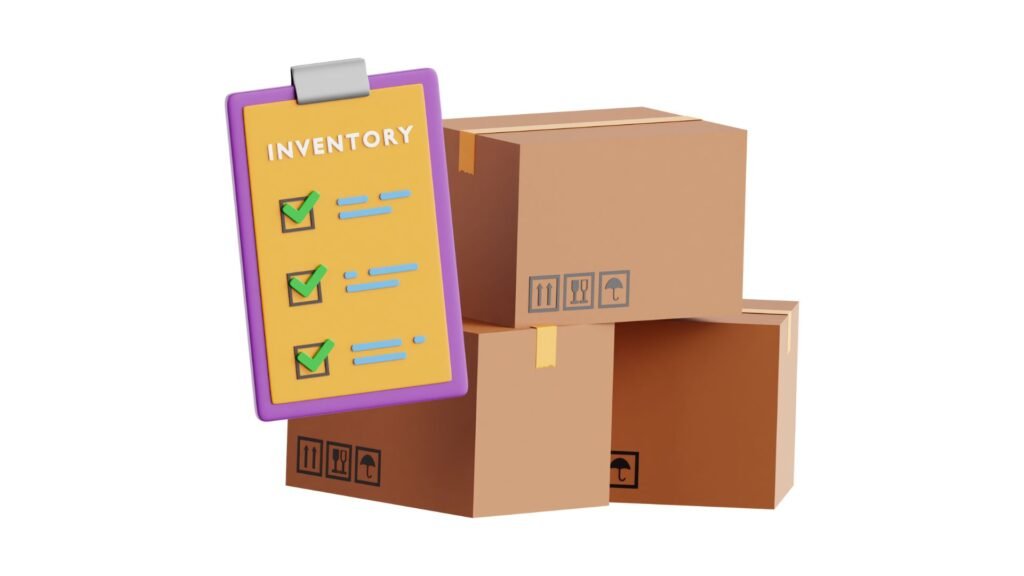
📊 Data-Driven Inventory Strategies
🧠 Harnessing Data for Smarter Inventory Decisions
Gone are the days when inventory was managed on paper and intuition. Today, smart businesses use data as a strategic asset. By analyzing historical sales trends, seasonality patterns, and supplier lead times, you can predict demand more accurately and avoid both stockouts and overstocking.
One retailer I worked with cut their excess stock by 25% simply by implementing a rolling 12-month demand forecast using past sales data and adjusting safety stock accordingly.
👉 Start with: Google Sheets dashboards, then graduate to tools like Power BI, Tableau, or inventory-specific platforms with forecasting modules.
📈 Analytics in Action: Inventory Techniques Backed by Numbers
Let’s talk techniques like ABC Analysis, XYZ Analysis (based on demand variability), and safety stock calculations—all of which depend on accurate data. For example:
- ABC tells you what’s most valuable.
- XYZ helps manage unpredictable vs. stable items.
- Combining them (AX, BY, CZ) gives a nuanced control strategy.
These methods aren’t just theory—they work. In one warehouse, combining ABC-XYZ reduced dead stock by 40% and improved service levels for A-items.
👉 Pro tip: Track and review KPIs like inventory turnover, order accuracy, and fill rate monthly to guide tactical decisions.
🧮 Precision Inventory: Techniques Using Real-Time Data and KPIs
With tools like barcoding, IoT sensors, and real-time dashboards, you can monitor stock levels, movements, and shrinkage as they happen. This allows you to:
- Set dynamic reorder points based on real-time demand.
- Identify slow-moving SKUs before they become liabilities.
- Instantly flag discrepancies between system and physical counts.
You should also align your actions with KPIs such as Days of Inventory on Hand (DOH) and Gross Margin Return on Investment (GMROI) to evaluate how efficiently your inventory is performing.
👉 Example KPI Benchmark: Aim for an inventory turnover ratio of 6–10 annually in fast-moving consumer goods sectors.
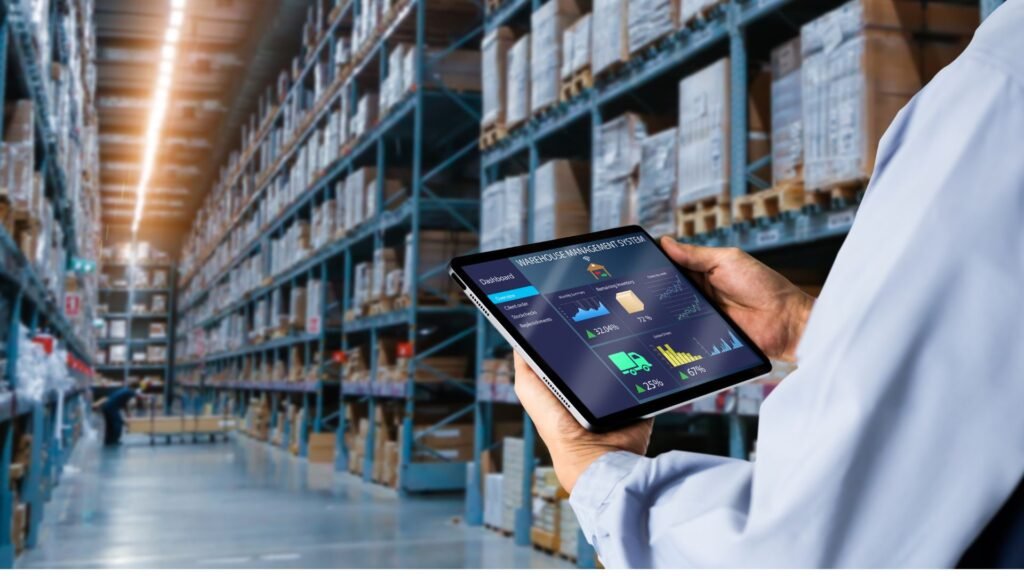
🏭 Operational Inventory Control
📅 Daily Discipline: Techniques for Effective Stock Monitoring
Inventory control isn’t just about big-picture strategy—it’s about consistent daily execution. Routine tasks like stock level checks, location audits, and bin accuracy help maintain data integrity and reduce shrinkage.
Adopt simple tools like:
- Daily cycle checklists
- Barcode scanners for real-time updates
- Google Sheets or mobile apps for instant reporting
These daily disciplines reduce reliance on major stocktakes and help catch discrepancies early.
👉 Tip: Assign daily checks by zone to ensure accountability and complete coverage.
🔁 Cycle Counting vs. Annual Stocktake: Which Technique Wins?
Annual stocktakes can be disruptive and prone to errors—especially in dynamic operations. That’s why cycle counting is considered the gold standard.
Method | Pros | Cons |
---|---|---|
Cycle Counting | Continuous accuracy, less downtime | Requires training and discipline |
Annual Stocktake | Snapshot overview | Costly, time-consuming, higher risk of shutdown |
Many companies implement ABC-based cycle counts, where Class A items are counted more frequently than B or C items.
👉 Best practice: Count A-items monthly, B-items quarterly, and C-items semi-annually.
📦 Reorder Point & EOQ Techniques to Prevent Inventory Gaps
Setting the right reorder point (ROP) and calculating Economic Order Quantity (EOQ) are critical to ensuring stock is replenished at the right time and in the right amount.
- ROP Formula:
ROP = (Daily Usage Rate × Lead Time) + Safety Stock
- EOQ Formula:
EOQ = √[(2 × Demand × Ordering Cost) ÷ Holding Cost]
These formulas balance the cost of ordering with the cost of holding inventory—minimizing total inventory costs.
👉 Pro tip: Recalculate EOQ and ROP quarterly to account for changes in demand, lead time, or costs.
🧠 Advanced Inventory Management
🤖 Next-Gen Inventory: AI, ML, and Predictive Techniques
Modern inventory management is evolving beyond traditional spreadsheets and manual oversight. Artificial Intelligence (AI) and Machine Learning (ML) now enable systems to:
- Identify demand trends and seasonal patterns
- Flag anomalies in real-time
- Automatically adjust reorder points and safety stock
Predictive inventory systems can analyze sales velocity, supplier performance, and external market indicators to anticipate stockouts before they happen.
👉 Example: A machine learning model can predict a spike in sales after a marketing campaign and prompt early replenishment.
🔮 Intelligent Inventory: Forecasting Techniques That Actually Work
Forget guesswork—advanced forecasting combines historical data, market intelligence, and real-time inputs to improve planning accuracy.
Key techniques include:
- Exponential Smoothing for fast-moving items
- ARIMA and regression models for multi-variable forecasting
- ABC-based demand forecasting for tiered inventory management
With the right model, businesses can reduce stockouts, avoid overstock, and fine-tune procurement cycles.
👉 Tip: Integrate demand forecasting with ABC classification for more tailored inventory planning.
🌐 Tech-Powered Techniques: IoT and Cloud in Modern Inventory Systems
The rise of IoT (Internet of Things) and cloud platforms has transformed how businesses manage inventory operations:
- IoT sensors track inventory levels, temperature, and location in real time
- Cloud-based inventory systems allow 24/7 access and team-wide collaboration
- Mobile-enabled dashboards provide on-the-go visibility into stock performance
These tools boost responsiveness, eliminate manual errors, and support multi-location management.
👉 Pro move: Use IoT tags for perishables, high-value items, or warehouse automation systems.
📦 Core Inventory Management Techniques – FAQs
Q1: What are the basic techniques for inventory management?
A: Key techniques include FIFO/LIFO, safety stock, reorder points, Economic Order Quantity (EOQ), ABC analysis, and stock audits. These foundational methods help maintain optimal stock levels and prevent overstocking or stockouts.
Q2: How often should I review my inventory?
A: It depends on your industry and sales velocity, but monthly or quarterly reviews are common. High-turnover businesses may benefit from weekly reviews and cycle counting.
Q3: What’s the difference between inventory control and inventory management?
A: Inventory control focuses on stock levels and storage, while inventory management includes forecasting, purchasing, and overall strategy.
📊 Data-Driven Inventory Strategies – FAQs
Q1: How can data improve my inventory decisions?
A: Data helps you track trends, identify fast or slow-moving items, monitor KPIs like turnover rate, and reduce costs by forecasting demand more accurately.
Q2: What KPIs are essential in inventory management?
A: Common KPIs include inventory turnover ratio, order accuracy, days sales of inventory (DSI), and carrying cost of inventory.
Q3: Can Google Sheets or Excel be used for data-driven inventory?
A: Yes. Templates with built-in formulas and dashboards allow you to visualize trends and calculate reorder points, EOQ, and ABC classification efficiently.
🏭 Operational Inventory Control – FAQs
Q1: What is cycle counting, and how is it different from a full stocktake?
A: Cycle counting involves checking a portion of inventory on a rotating schedule, reducing disruption and errors compared to annual full inventory audits.
Q2: How do I set a reorder point?
A: The reorder point = (Average Daily Usage × Lead Time) + Safety Stock. This formula ensures you reorder before stock runs out.
Q3: What is EOQ, and why does it matter?
A: Economic Order Quantity (EOQ) is the ideal order quantity that minimizes total inventory costs (ordering + holding). It’s crucial for cost efficiency.
🧠 Advanced Inventory Management – FAQs
Q1: How does AI differ from traditional forecasting methods?
A: AI dynamically learns and adapts from new data, while traditional methods rely on fixed historical averages and are less responsive to changes.
Q2: Can small businesses afford advanced inventory tools like predictive analytics or IoT?
A: Yes. Many cloud-based platforms now offer scalable pricing and features. Even low-cost solutions like Zoho Inventory, Katana, or DEAR Systems offer predictive tools.
Q3: Is cloud-based inventory better than on-premise systems?
A: For most businesses, yes. Cloud systems offer real-time access, easier updates, mobile access, and integrations with e-commerce, ERP, and POS systems.